传热 在蒸汽加热系统中,产生和输送蒸汽的唯一目的是在制程的换热器表面提供热量。如果知道了需要输入的热量和蒸汽的压力,则可以确定所需的蒸汽量,这样就可以确定锅炉和蒸汽输送系统的大小。 传热的模式 无论是在一种介质或不同介质之间,只要存在温度梯度,传热就会发生。热量传递的方式可以是导热、对流或辐射。 导热 当固体或静止的流体介质中有温度梯度存在,热量就会以传导的方式传递。当流体中相临的分子碰撞时,热量从能量较高的分子传向较低的分子。高温总是伴随高的分子能量,导热的方向是温度下降的方向。 液体和气体中都会发生这种现象。在液体中因为分子之间更加靠近,分子间的相互作用更加强烈和频繁。在固体中,导热是由晶格振动形式的原子活动引起。 用于描述导热的传热公式称为傅立叶定律。这是一种在稳定状态下线性温度分布,对于一维平板壁面,它表示为:
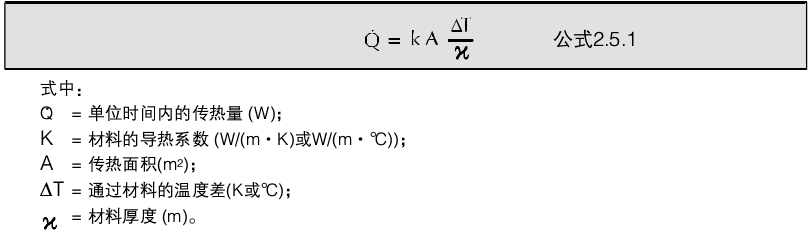
例2.5.1 对于一块铁板,铁的导热系数为70 W/(m·℃) 度为1500C,另一侧为800C
铁板的厚度为25mm,面积为0.3m乘0.5m,一侧的温 传热量为:传热量=70W/(m·0C)x(0.3x0.5)m2x (150一80)℃ 0.025m 传热量=29400W(29.4kW)
导热能力是平板材质的特性,它和温度有关系。表2.5.1表示各种常用材料的导热系数随温度的变
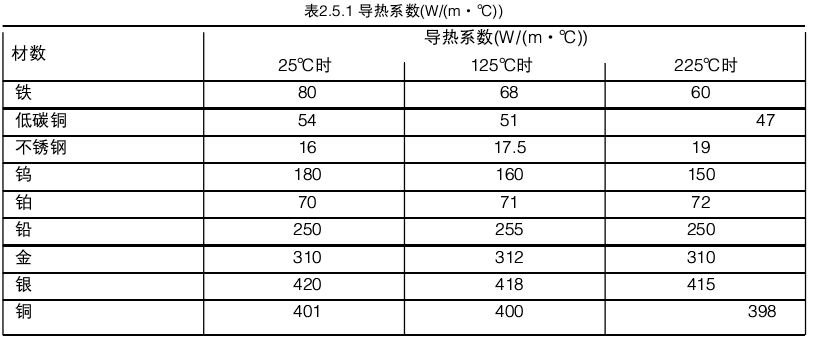
根据热量传导的机理,一般固体的导热系数要远大于液体的导热系数,液体的导热系数要大于气体的导热系数。空气的导热系数特别低,这就是为什么很多隔热材料都含有大量空气空间。 对流 不同的温度下的换热表面和流体之间的热量传递称为对流。其机理实际上是一种分子扩散和规模运动组合。 在表面附近流体流速低,扩散(分子随机运动)占主导。但离开表面,分子规模运动的影响增加。对流传热有强制对流和自然对流两种方式。强制对流出现在流体的流动由外部力量驱动,如泵或搅拌器。相反自然对流是由于流体中温度的变化导致密度的不同而产生的浮力引起。 由于物体的相变,如蒸发或冷凝而引起的热量传递也归为对流传热模式。 例2.5.2 考虑一个换热面,面积为。.4m乘。.9m,温度为200C 0 流过表面的流体的主体温度为500C0 对流传热系数(h)为1600W/(m2·℃)。 确定传热量: 传热量=1600W/(m2·0C) x (0.4 x 0.9)m2 x (50-20)0C 传热量=17280W(17.28kW) 辐射 物质从表面以电磁波的形式发射热量的传递方式称为辐射。由于没有中间介质存在,这是两个不同温度表面的净热量传递。这种形式的热量传递不依靠中间介质,实际上在真空状态下效率*佳。 总传热方程 在大多数实际情况下,热量只通过一种方式传递的情况很少存在。总的传热过程通常是两种或多种传热方式的结合。 总的传热系数(U) 总的传热系数考虑了被换热面隔开了的两种流体之间的导热和对流。总的传热系数是总的传热热阻的倒数一总的传热热阻是各分项传热热阻之和。 总的传热系数还需要考虑换热过程的结垢程度,在换热表面水膜和污垢的积聚将大大降低传热效果。 结垢因素表示了由于流体的不纯净、铁锈的形成或流体和换热面发生反应而产生的附加热阻。 各个系数的大小取决于换热过程的特点、流体的物理性质、流率和换热表面的物理布置等因素。 因为在换热面积确定之前其物理布置无法确定,因此换热器的设计通常采用交替迭代的过程。这种过程的起点通常对典型的换热器选择一个常用的总传热系数。 精确计算各个传热系数是一个复杂的过程,在很多情况下由于一些参数无法知晓而不能进行,因此从实际考虑看,选择一个合适的总传热系数是一种可行的方法。 温差A丁 牛顿冷却定律表示传热量和冷热流体之间的瞬时温度差有关。在传热过程中,温度差随时间和地点而变化。总的传热公式是牛顿冷却定律的延伸,平均温度差用来确定对于给定的热负荷所需要的换热面积。
平均温差A丁M 平均温差的定义在不同的流动形式过程中而不同,例如在换热器中它取决于流动的方向。一次侧和二次侧流体的流向可能是同向(平行流//lll}流)、相反方向(逆流)或垂直(交叉流)。因为传热的热量只是相变的结果,当蒸汽作为一次侧加热介质时,温度可以认为是恒定的,温度的分布不再取决于流向。 但是,二次侧流体流过换热面时,*高的传热率出现在进口,然后沿着流程不断下降,在出口处*低,这是因为随着二次侧流体温度的上升蒸汽和二次侧流体之间的温度差不断减小。典型的蒸汽和二次侧流体的温度分布
二次侧的温度上升是非线性的,对数形式能*好表达该分布。因此平均温差采用对数平均温差或 LMTD或t'TLM o 一种简单但不太精确的计算平均温差的方法是使用算术平均温差或AM丁D或4丁AM。考虑二次侧流体的温度呈线性分布,可以快速手工计算。用公式2.5.3计算的平均温差可以得到比较满意的近似值。算术平均温差的分布
公式2.5.4和2.5.5都假定比热或总传热系数没有变化,也没有热量损失。现实情况是,随温度的变化比热有所变化。由于流体特性和流动工况的变化,总的传热系数也有所变化。但对于大多数应用来说,这种变化可以忽略不计,使用平均值能得到很好的结果。 在很多情况下,换热设备有保温措施,但不可能达到100%的保温效果,因此在蒸汽和二次侧流体发生的热量传递不是蒸汽损失能量的全部。 例2.5.3 使用2 bar g的蒸汽将水从20℃加热到500C0 2 bar g下饱和蒸汽的温度为1340C . 因为和两种流体的温差相比,二次侧流体的温度上升很大,两种计算方法得到结果的差别很大。 使用算术平均而不使用对数平均,得到的换热面积比需要的小15%0 传热的热阻 在传热过程中金属墙不是唯一的热阻。在蒸汽侧可能有一层空气膜、冷凝水膜和污垢层。 可能有粘在换热面上的产品层或污垢层以及迟滞不流动的产品层。 对产品进行搅动可能消除迟滞层的影响,经常清洗产品侧可以减少污垢层。 虽然如果能经常清洗蒸汽侧表面可以减少污垢层厚度而提高传热率,但并非总是可能的。 重视锅炉的正确,同时将蒸汽中携带杂质的水分去除,可以大大降低污垢层的影响。 在产品侧. 膜状凝结 冷凝水膜的消除并非如想像那么简单。蒸汽冷凝释放出蒸发烩,水滴在换热器的表面形成,这些水滴结合在一起形成连续的冷凝水膜。冷凝水膜的热阻是不锈钢换热面的100150倍,是铜的500600倍。 滴状凝结 如果换热器表面的水滴没有马上合并就会形成非连续的冷凝水膜,就会产生“滴状凝结”。在滴状凝结状态下达到的传热率要远高于膜状凝结状态下的传热率。 如果换热器表面大部分处于滴状凝结,那么传热系数比处于膜状凝结大10倍。如果换热器能设计成处于滴状凝结,那么它产生的热阻和其它热阻相比可以忽略不计。但是维持滴状凝结状态是很难达到的。 如果换热器表面涂有防湿的材料,换热器有可能在一段时间内维持滴状凝结。为了形成滴状凝结,很多换热器表面涂有机硅树脂、聚四氟乙烯、蜡和脂肪酸类涂层。但由于诸如氧化、结垢等原因,这些涂层将逐渐失去功效,*终膜状凝结将占主导。 因为空气是良好的绝热体,它提供了更大的传热热阻。空气的传热热阻是钢的15003000倍,是铜的8000 16000倍,这表示0.025 mm厚的空气层相当于400 mm厚铜壁产生的热阻。当然这些相对关系取决于每一层的温度分布。 图2.5.4表示了各传热热阻层对传热过程总的影响。这些传热热阻不仅增加了整个导热层的厚度,同时也大大降低了各层的平均导热系数。 热阻越大,温度梯度越大,这表示为了达到同样的产品温度,需要更高的蒸汽压力。 在制程和空间加热应用中,换热器表面空气膜和冷凝水膜普遍存在,实际上在所有的蒸汽加热设备中都有不同程度的存在。为了达到理想的产品输出和*小费用,减少冷凝表面的各膜层厚度以维持高的传热性能是一种有效的方法。事实上,空气对传热效率的影响*大,如果能从供给的蒸汽中排除空气能大大提 高加热性能。 和传热*有关的5个术语为: 1.热流量Q (W) 2.导热系数k (W/(m·℃)) 3.热阻系数r ((m·}C )/W ) 4.热阻R ((m2·}C)/W) 5.传热系数U (W/(m2·℃)) 接下来的本章节内容对它们及其之间的相互关系作阐述。 计算通过平板的传热量传统上使用总传热系数“U",或更正确的是使用平板两侧流体间的总传热系数。"U”值的变化范围很大,它跟材料和流体有关,受经验数据和操作经验影响。前面提到的冷凝水膜、空气层、污垢层和金属壁另一侧的产品对总传热系数均有很大影响,因为这样,我们首先考虑通过单层平板的传热,然后再考虑多层平板的情况。 通过单层平板的传热 我们可以从*简单的例子开始,一面金属墙,热力性质均匀,并具有特定的表面温度。 通过多层障碍物的热流 如图2.5.4所示,换热器的管子或板片为蒸汽加热水的金属壁,同样存在其它不同的障碍物诸如空气膜、冷凝水膜、污垢层以及水侧和换热面相临的迟滞的水层来阻碍热量的传递。这些膜层类似污垢层阻碍热量传递,换热器设计者采用“污垢系数”考虑其对换热的影响。所有这些膜层,附着在金属壁的热阻上,组成热流的阻力,如电流的电阻,这些热阻形成总热阻。 导热系数的大小取决于膜层的材料(和温度)。例如,空气的热阻是水的热阻30倍。基于这个原因,在蒸汽达到用汽点前除去空气比除去蒸汽中的水分更加重要。当然,与此同时去除蒸汽中的水分也很重要。 空气的热阻大约是钢的热阻2000倍,是铜的热阻20000倍。因为空气和水的热阻要远远高于钢和铜的热阻,因此对于传热的总热阻来说即使很薄的空气膜和水膜影响也很大。 如果空气膜和水膜存在,将传热系统的材料由钢改成铜作用不大,例2.5.5显示材料的改变所带来的性能改进效果微乎其微。通过良好的工程实践,例如在控制阀的进口蒸汽供给管道上安装汽水分离器和浮球疏水阀组可以消除空气膜层和水膜层,同时安装过滤器可以减少污垢层的厚度。 处理产品侧的污垢层有点困难,但定期清洗换热器有时是一种解决方法。另外一种减少结垢的方法是让换热器运行于低压工况,这样可以降低蒸汽温度,减少产品中的结垢现象,这种方法特别适用于产品介质是溶液的情况,如牛奶。 例2.5.5 考虑一个汽水换热器蒸汽侧空气膜、冷凝水膜、污垢层为0.2 m m厚,在水侧水膜和污垢层分别为0.05mm和0.1 m m。换热面钢板的厚度为6 mm. 可以看到和钢相比,铜的导热系数要远大于钢的导热系数,但因为空气和其它结垢因素对传热的影响占主导作用,所以改用铜以后对总传热系数的影响很小。 请注意在实际应用中其它因素也影响总的U值,如通过换热器管束或平板的蒸汽和水的流速以及对流和辐射换热的综合影响。 同样,安装了汽水分离器和过滤器后也不可能完全消除蒸汽侧空气、冷凝水和污垢。以上计算只是突出这些因素对传热的影响。但是,任何消除这些障碍的措施都会有很大的效果,只要采取了这些措施,蒸汽设备的换热效果会立刻提高。 不需要计算各个单独的热阻,已有的表格列出了各种不同型式换热器总的传热系数U值,例如加热水或油的蒸汽加热盘管,这将在2.10中介绍。 换热器U值受很多因素的影响,例如设计(管壳式或板架式)、结构材料和流体介质,因此变化很大。 以上内容由彪维公司(www.bilwe.com)编写,转载请注明文章出处。 |